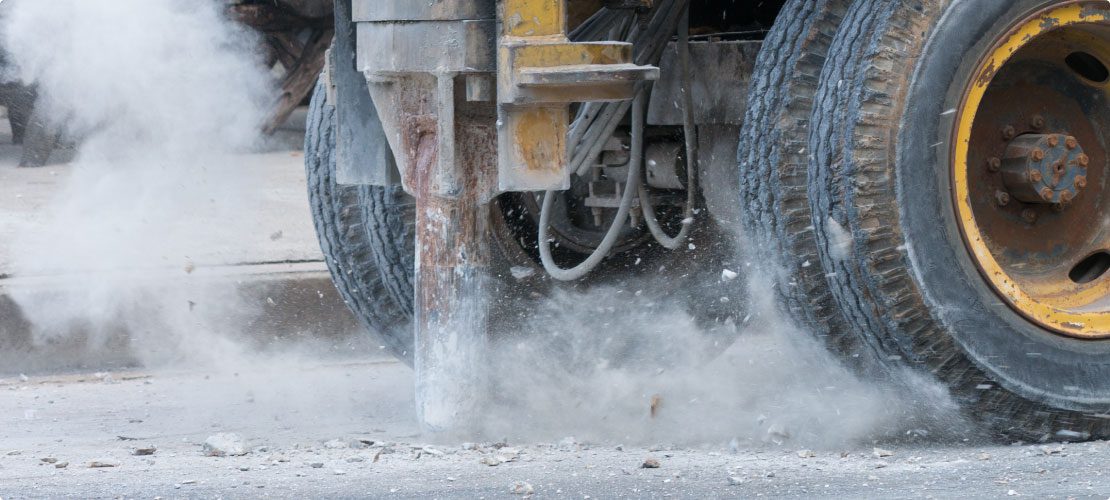
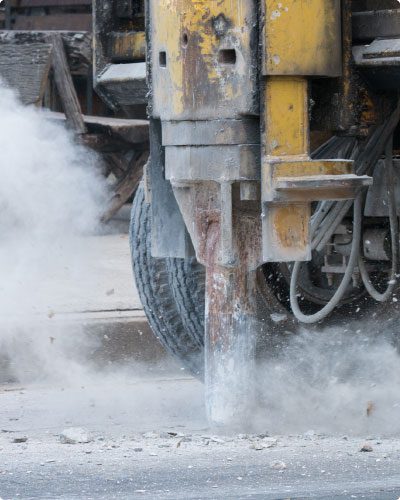
The construction industry has a dust problem. Tiny invisible crystalline silica dust to be specific. Although it wasn’t deemed a problem in the past doesn’t mean it didn’t exist. The difference between then and now is there are reams of studies, tests, and evidence from various educational and government sources proving it.
The issue is about protecting employees and the surrounding community. Merely handing staff personal protective equipment (PPE) and a hose doesn’t solve it. You can give your employee a respirator, but what about the people with chronic breathing issues down the road? You can hose down areas, but what if the silica is already in the air?
DustBoss cannons are specifically designed to address silica dust control in the construction industry. They do this by introducing millions of atomized mist droplets that collide with minuscule airborne particulates and pull them to the ground at the point of emission, protecting both employees and the surrounding community. Moreover, atomized mist helps mitigate the expensive fines and shutdowns associated with construction dust emissions guidelines from the Environmental Protection Agency (EPA), the Occupational Safety and Health Administration (OSHA), and municipal permits.
SILICA DUST COMPLIANCE: HOW WE GOT HERE
Silica – and the chronic condition “silicosis” – has been recognized since 1700, but nothing was done about it until the 1930s when the Hawks Nest tunnel construction project became the site of one of the worst industrial disasters in U.S. history.[1] Hundreds of workers died from silicosis while building the tunnel and another 1,500 were reported to have contracted the disease within two years of working on the project.
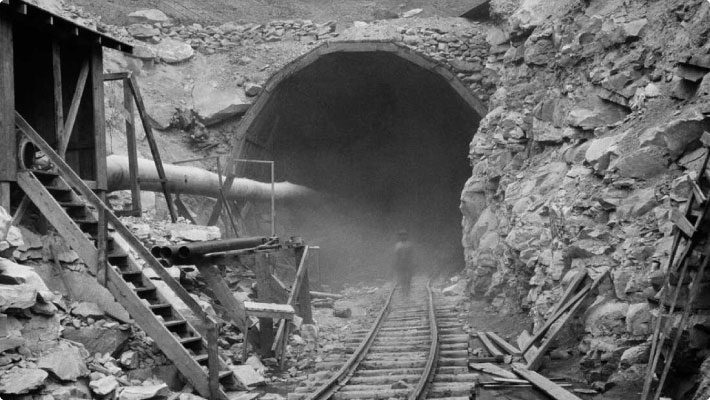
Image courtesy of Elkem Metals Collection, West Virginia State Archives
It wasn’t until 1996 that the United States Secretary of Labor emphasized a focus on silicosis. In 2013 -- 83 years after Hawks Nest -- the US Occupational Safety and Health Administration (OSHA) issued silica rules for construction aimed at curbing lung cancer, silicosis, chronic obstructive pulmonary disease, and kidney disease associated with worker exposure to crystalline silica.[2] Approximately 2 million U.S. workers remain potentially exposed to respirable crystalline silica.[3] This tells us that the traditional solutions to dust control (hoses, sprinklers, local exhaust ventilation, etc.) aren’t enough.
What does this all mean? It means the problem is very old, the regulations are very new, and the more research is produced, the more we realize that the old strategy of assigning a person with a hose to solve the problem doesn’t work on airborne microscopic particles. That’s where mist cannon technology steps in.
WHAT CONSTRUCTION ACTIVITIES CAUSE SILICA DUST EMISSIONS?
An extensive study by researchers from IRRST in 2013 titled, Construction Workers’ Exposure to Crystalline Silica compiled data from National Institute for Occupational Safety and Health (NIOSH) of the United States, the Institut de veille sanitaire (InVS) of France, and the American Conference of Governmental Industrial Hygienists (ACGIH) construction committee. Researchers said, “The tasks and tools with the highest exposure (all more than twice the regulatory value during the duration of the task) are, in decreasing order: sawing masonry with a portable masonry saw, bush hammering, breaking pieces of masonry (chipping jackhammers on concrete or ceramic), tunnel boring (tunneling machine), and brick/stone joint grinding (tuck point grinding).”
These aren’t the only activities that cause emissions, and some substances produce more silica emissions than others. [Fig.1] However, in the absence of wind, the substance itself doesn’t shed much without a specific activity causing fugitive emissions.
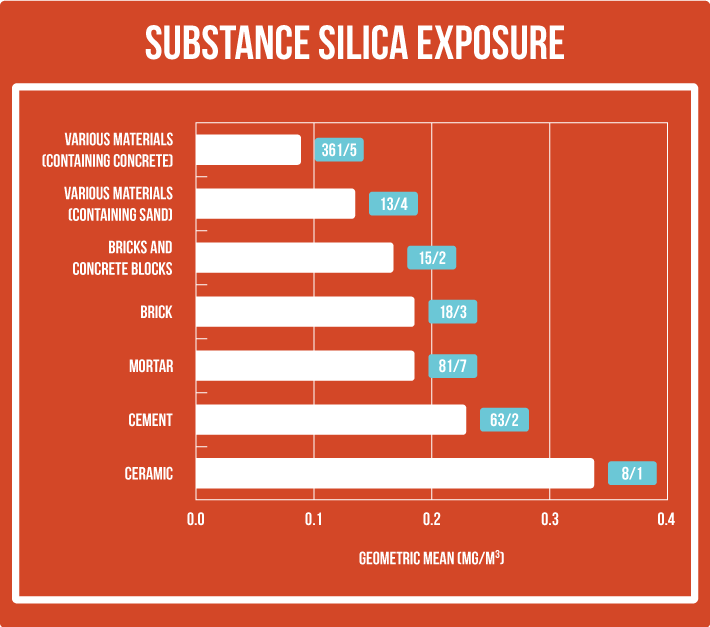
[Figure 1]: Silica dust exposure by substance.
There are very specific features of some activities, such as concrete cutting, that OSHA provides detailed instructions on. Other activities fall under general employee exposure guidelines that are at or below the permissible exposure limit (PEL). Dust volumes in an area are measured by weight in micrograms (µg) per cubic meter (m3). The OSHA guidelines limit employee exposures to a PEL of 50 μg/m3 as an 8-hour time-weighted average (TWA).
Several construction activities cause crystalline silica emissions:
- Demolition – High reach hydraulic clamps, falling material, concrete surface/foundation removal, etc. all create a tremendous amount of dust in general.
- Soil remediation – Soil samples from an environmental assessment may reveal contamination from previous activities on the site requiring the toxic soil to be removed and properly disposed of. Emissions from the removal, storage, and loading of this soil is strictly controlled and monitored.
- Excavation – Tunneling, deep excavation to create parking garages, and other subterranean activity can expose geological layers of high crystalline silica substances such as clay, limestone, etc. From digging to loading, these emissions must be controlled.
- Storing – Piles of dry and dusty substances, even if covered overnight, can release emissions once disrupted for loading and transport.
- Cutting, grinding, shaping, finishing – Equipment for concrete work might be accompanied by a “local exhaust ventilation.” Even with ventilation on wetted surfaces, these activities can exceed OSHA PEL. Concrete cutting, if not done with technology that automatically wets the blade according to OSHA guidelines, also falls under this category.
- Recycling – C&D (construction & demolition) recycling is an essential part of controlling the amount of waste that goes into landfills. Recycling involves separating materials into large storage piles and then either transporting the C&D to a recycling plant or crushing it on site before reuse. Wind, disruption from heavy equipment, loading, and processing are all sources of dust.
OSHA violations apply to the air quality of the workplace, but municipal permit and EPA violations happen when the dust leaves the site line and people start submitting complaints to various agencies. Testing methods for these substances vary by agency, but for the most part, it is done with a gravimetric meter set up outside the site line or with a personal measuring device attached to workers throughout their shift.
READY FOR A QUOTE?
Talk to a dust control specialist and get a quick quote for your project.
SILICA DUST EMISSIONS FROM CONSTRUCTION
Dust size is measured by width in micrometers or microns (µm). Particulate Matter (PM) as large as 200µm is able to remain airborne on normal ambient air currents and is no longer visible to the naked eye the smaller it gets. At the size of <PM10 (the regulated size threshold for airborne crystalline silica particles), the dust is able to avoid the body’s natural defenses, penetrating deep into the lungs and causing silicosis. [Fig. 2]
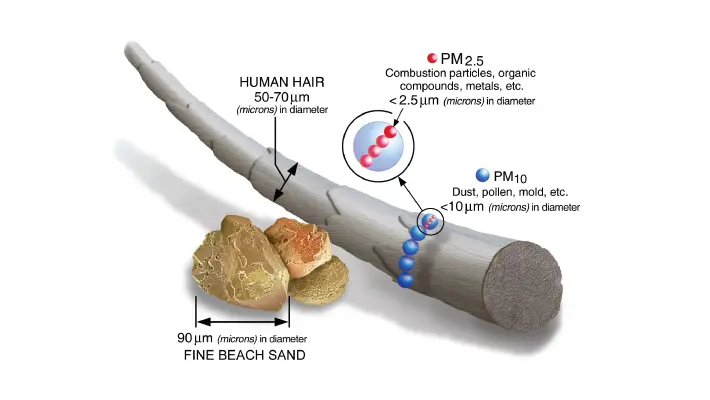
[Figure 2]: Particle size comparison.
(Image courtesy of the U.S. EPA)
Field tests have shown that droplet sizes need to be roughly the same size as the airborne particulates to be effective. Airborne suppression of outdoor emissions is typically accomplished using water. Hoses and sprinklers create droplets between 200µm and 1000µm compared to atomized mist which is sized in the range of 15µm to 200µm. Droplet sizes greater than 200µm are only adequate for wetting surfaces, but don’t offer airborne dust suppression. This is due to the slipstream effect.
As a droplet moves through the air, the mass creates a strong current of air that moves around it called the slipstream effect. Particles get caught in the slipstream and remain unaffected. In some cases, the droplet can even lift the smallest particles, making the issue worse. Atomized droplets, on the other hand, travel with the particles, collide with them, and drag them to the ground. [Fig. 3]
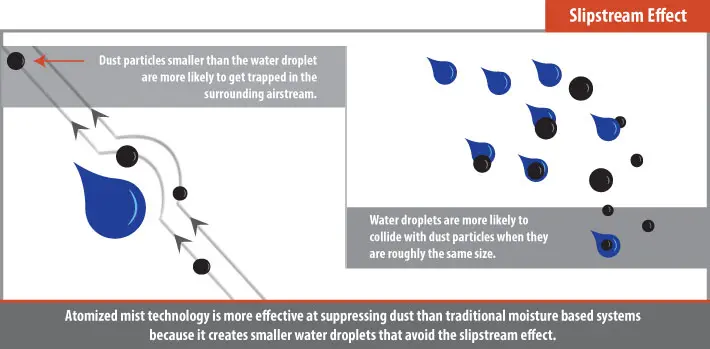
[Figure 3]: Water droplets and the slipstream effect.
Why are hose and sprinkler droplets so large? Water propelled through hoses produces larger droplets, because it depends on the water pressure to propel the droplets long distances. Thus, the sheer volume needed to propel the water creates larger droplets. In contrast, an atomized misting cannon relies on a powerful fan to propel smaller droplets created by misting nozzles, using far less water and offering more complete coverage.
SILICA DUST CONTROL IN THE CONSTRUCTION INDUSTRY
Misting systems for silica dust control come in different sizes and configurations, depending on the total area in need of dust control and the application. Regardless of size, atomized misting cannons work off the same general concept; a powerful fan in the back of a heavy-duty cone-shaped barrel pushes air through the barrel toward a misting ring manifold mounted in front. Pressurized water is forced through the manifold and fractured into a fine mist by specially designed nozzles. The forced air propels millions of tiny droplets toward a designated spot or an area when oscillation is utilized. Two systems in the DustBoss line diverge from that design, the DB-60 Surge® and the DustBoss Atom®.
The DB-60 Surge combines the power of an industrial fan, misting ring, and barrel with the reach and force of a central high-pressure spray nozzle. This offers the versatility and high reach needed to meet the demands of varying demolition projects. The pressurized spray resists wind shear and even uses the force of the wind to further fragment and carry the droplets, enhancing its dust suppression capabilities. This is achieved without the need for the high-water output associated with a hydrant-dependent hose or industrial sprinkler system.
The DustBoss Atom is a compact self-contained mobile unit for spraying pressurized water powered by a 9.1 HP diesel engine. Water pressure is boosted by a pump rather than relying on pressure from the hydrant, throwing the stream 30 meters (~100 feet) using only ~26 lpm (7 gpm). The unit’s 0-65º vertical adjustment and 100º maximum oscillation range increase the coverage area to 567 sq/m (6,100 sq/ft). This means the design offers indoor and outdoor dust control with less wastewater runoff and standing water than hoses, while still allowing the machine to be distant from the water source.
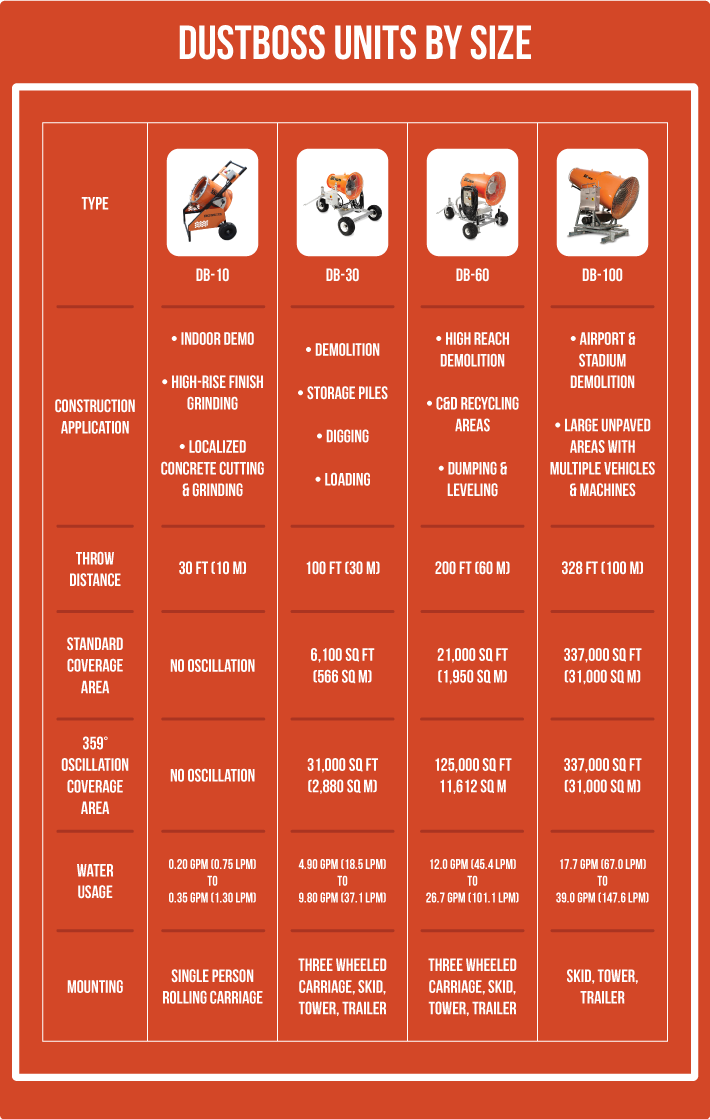
[Figure 4]: DustBoss dust suppression system features comparison by unit size.
DUST CANNONS IN CONSTRUCTION
One of the ways to guarantee a compliant demolition contractor is if they have a dust cannon(s) as a standard part of their equipment portfolio. Depending on the size of the construction project, best practices are for the general contractor to also have dust cannons available to specialist contractors (such as retaining wall builders, pavers, and masonry) for each phase of the project, even after demolition.
As you can see, outdoor industrial atomized dust control of crystalline silica not only protects workers but the surrounding community and the bottom line. Buying versatile dust control machines reduces the chance of violations. The machines are a visible queue to people passing by and showcases the company’s commitment to community safety.
Our experts can work closely with project managers and environmental managers to examine each phase of the construction plan, identify potential dust exposures, and recommend dust mitigation strategies. Contact us today for a project assessment and support in creating a dust control plan.
CREATE A DUST CONTROL PLAN TODAY!
Receive a FREE site analysis and talk to a dust control specialist to fight silica dust!