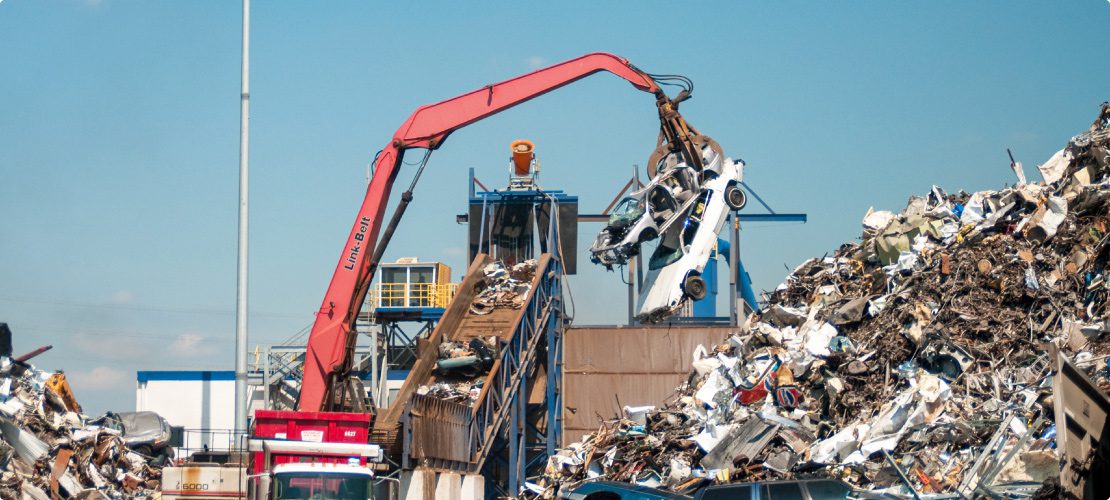
The scrap recycling industry is growing proportionally with the population and the subsequent volume of waste. At the same time, commercial and residential expansion is encroaching on scrap recycling operations that once enjoyed relative isolation or were occupying exclusive industrial zones. In some cases, the new dynamic has caused changes in permits and local codes around dust emissions and wastewater runoff.
It is undeniable that scrap recycling is one of the most important industries in the United States, accounting for more than half of the U.S. metal supply by weight and roughly 40 percent by value. From vehicles to appliances to construction and demolition (C&D) waste, it is a necessary industrial process with a highly beneficial environmental outcome.
Society wants less waste going to landfills which requires more scrap recycling, leading to expanding processes with the unfortunate outcome of more fugitive dust emissions. Juxtaposed with society’s desire for affordable housing, there is an inevitable clash of needs. Rather than moving well-established operations, scrap handlers implement dust suppression methods such as atomized mist to control airborne emissions.
WHAT IS SCRAP RECYCLING DUST?
Here’s the problem: every scrap material has its unique properties. The old methods of hosing down piles and lining open-air scrap yards with trees still help but no longer meet strict compliance standards.
Understanding the properties and why the scrap emits dust particles helps inform the type of dust control each substance may need to apply the proper dust suppression methods. For example, utilizing surface suppression on scrap metal piles prior to disrupting them may be a more effective dust control solution than surface suppression on concrete piles, since densely packed concrete is more likely to release particulates once the surface is broken.
PARTICLE SIZES
Common dust suppression methods like hoses don’t sufficiently address airborne emissions of small particulates due to large droplet sizes and the slipstream effect. Regulators test for particulate matter (PM) sizes that are too small to see, measuring between 10 microns (μm) and 2.5μm (commonly noted as PM10 to PM2.5). These sizes are invisible to the naked eye and are common during silica emissions from concrete or heavy metals emissions. The inhalation of fine particulates poses greater human health risks due to its ability to build in the respiratory airways, irritating existing breathing conditions. Smaller particulates can penetrate deeper into the lungs, creating chronic breathing problems or enter the bloodstream, causing damage to internal organs.
READY FOR A QUOTE?
Talk to a dust control specialist and get a quick quote for your project.
STATIC PROPERTIES
Wind, movement during transport, or atmospheric electrostatic conductivity can create static properties in some materials. Material on material friction created by demolition, storage, transport, and processing can also increase the attraction of dust particles. Static properties in dry materials are greater than those in wet materials.
STATIC AND DUST PARTICLES
There is no practical way for scrap recyclers to avoid static. The greater the volume of dust in an area, the larger the amount of dust that clings to statically charged objects.[1] Statically charged material will attract atmospheric dust not produced by the operation and then release it upon disruption, however, the operation is still responsible for all emissions. Not only can it leave the site line, charged particulate dust can be attracted to machinery within the operation and reduce the operating life.[2] This is why consistent airborne and surface suppression is important. As dry airborne dust encounters various statically charged objects, it takes on a positive or negative static electric charge. Dust particles with a positive electrical charge are attracted to surfaces with a negative electric charge and vice versa.
MAGNETIC SURFACES ATTRACTING PARTICULATES
Some metals such as steel, iron, and nickel can have magnetic properties that attract some types of fine heavy metal particulates that are considered toxic. Most metal scrap is categorized as ferrous (containing iron and magnetic) or non-ferrous (not-containing iron, not magnetic). Even when a scrap recycler or demolition contractor takes measures to control heavy metal emissions, ferrous substances could be attracting some heavy metal particulates and transporting them to storage and piling areas.
SCRAP DUST AND COMPLIANCE
As sites become closer in proximity to populated areas, permits become more stringent about air quality during scrap generation, storage and processing activities. Although the locations of demolition sites can change, recycling facilities are static. It is residential and commercial growth that encroaches on a site, causing complaints and violations. To enforce these permits, regulators have been known to test soil, water, and/or set up gravimetric dust monitors as far as a mile upwind and downwind from the site to test emissions.
Proper control of scrap dust, particularly heavy metals and silica, requires identifying problem areas and implementing dust suppression methods that addresses each area based on the type of emission. Without a robust and comprehensive dust control plan, the consequences could be:
- OSHA violations
- EPA and local government fines
- Significant downtime or closure of operations
- Lawsuits and expensive legal settlements
CASE STUDY: HEAVY METAL DUST IN THE SNOW[3]
In 2020, researchers discovered that a scrap recycler located in southeast Winnipeg, Manitoba, Canada was emitting 5x the legal limit of heavy metal for industrial areas and 20x for residential areas. The samples were taken from the snow around the facility and up to several kilometers away. This sparked a potential class-action lawsuit by residents and commercial neighbors.
Located in an industrial area upwind from a low-income community consisting of 58,520 residents, the scrap recycling facility processed an estimated 178,500 tonnes (196,800 tons) of scrap from vehicles and other sources annually. The surrounding area also consists of other mixed industrial, commercial, and residential land uses within the 24.5 km (15.25 mile) reach of detection.
Researchers found high concentrations of Zi and Pb along fencing surrounding the site. Further investigation indicated the shredder area was the most contaminated area for heavy metals, notably for Pb, Zn, Ni, Cr, Cd, and Hg, decreasing with the distance from this source to low or moderate levels in nearby residences. The study notes that prevailing wind direction plays “a significant role in the dispersion and deposition of industrial emission of heavy metals in accumulated snow cover.”
In the industrial zone, concentrations of heavy metals were found to be significantly higher with the next highest being along the roadside, then the commercial zone, and finally the residential zone. With this information in hand, further tests were needed to determine if there was a significant health risk to surrounding populations.
Proper control of airborne PM10 and PM2.5 heavy metals can be achieved with the correct, strategically placed atomized mist technology. This helps scrap recycling facilities avoid violations, fines, and expensive litigation by preventing particulates from migrating beyond the immediate area.
DUST CONTROL IN THE LIFECYCLE OF SCRAP
Once the material is removed from its original service, it is considered scrap. Most scrap containing highly toxic substances like asbestos is not recycled. Recyclable scrap can still have its own unhealthy and regulated properties, which can be spread through the scrap material’s entire lifecycle in the form of dust emissions.
The best method for controlling both surface and airborne scrap dust is atomized mist. The mist consists of millions of tiny droplets that are introduced into an area by cannon or pressurized sprayer. Cannons use a powerful fan and misting ring configuration to control particulates. Atomized misting heads and sprayers use water pressure to deliver dust suppression. The size and model of each method depend on the application.
SCRAP DUST IN DEMOLITION
Indoor Operations – When there’s a presence of asbestos, lead, or cadmium, often demolition needs to be done “surgically” by hand or mini-excavator. For these types of projects, a small dust suppression cannon like the DustBoss DB-10 or a dust suppression system like the DustBoss Atom can protect workers and prevent emissions.
Outdoor Operations – Taking down large outdoor structures can generate a tremendous volume of airborne dust of all kinds. This activity requires larger machines such as the DustBoss DB-30 or DustBoss DB-60 which can be vertically adjusted to reach high up or oscillate to cover wide landing zones.
SCRAP DUST FROM STORAGE PILES
Outdoor storage – Atomized mist droplets travel with dust particles, even in windy conditions, and pull them to the ground. Mist cannon sizes vary and the best option depends on the height of the pile and the size of the coverage area. Some scrap recyclers with sizeable scrap storage areas use a tower-mounted dust cannon to reach over tall piles of scrap as the tops of piles are more exposed to wind and dust emissions can travel farther.
Indoor storage – Some scrap facilities have different covered areas or barns where specific types of scrap have been separated and stored. However, when these piles are disrupted, it can kick up a lot of dust. Many operators have chosen a misting head like the DustBoss DB-M Mini to control dust, which can be triggered if there is activity in the area.
DUST DURING SCRAP TRANSPORT
Port – There are two main methods of loading scrap onto a barge or into the hold of a cargo ship: conveyor or crane with a claw or magnet attachment. An effective dust control method can reach the height of the crane and the beam (width) of the cargo vessel. With a long reach and wide oscillation, the DustBoss DB-60 offers a long effective cone of mist that travels with the windy conditions commonly found in waterways.
Ground – Covered trucks are the best option for dust control in transporting scrap since they pass so many different areas. A central issue is the amount of dust kicked up from tires as they enter and exit the site. Having a dedicated wide area cannon like the DB-30 for atomized dust suppression covering the loading and unloading area will mitigate the dust caused by vehicles. Hosing down the ground can cause pooling and excessive runoff. The tiny droplets from the atomized mist cannon offer airborne dust control and surface suppression with little to no pooling or excessive wastewater runoff, making it more compliant and safer for walking and small vehicles.
SCRAP DUST AT RECYCLING FACILITIES
Crane separation – Using a crane magnet or claw can cause disruption deep in piles causing dust and then producing a path of airborne dust high in the air as material is moved from the pile to the destination (truck, barge, separator, conveyor, etc.). A misting cannon like the DustBoss DB-60 has the reach and the optional oscillator to offer superior airborne dust control.
Vibrating grates – Separation of fines through vibrating grates is a way to collect higher-worth non-ferrous metals, however, the vibration can create copious amounts of dust. Mounting misting bars along the vibration path or strategically placed DustBoss DB-M Mini misting heads can help prevent dust from leaving the separator.
Separation lines – To ensure all fines and scrap are properly separated, some operations have trained people standing at conveyor belts who can identify metals and ensure they are properly sequestered. Worker exposure to heavy metals is serious and heavily regulated by OSHA. Strategically placed DustBoss DB-30 fog cannons reduce airborne dust emissions, providing a safer workplace.
Processing – Crushers and shredders can quickly process an entire vehicle but also emit the dust contained within. Recyclers have placed misting heads around the processor and mounted oscillating DustBoss cannons to cover the area both for workplace safety and to mitigate any fugitive PM10 and PM2.5 that might escape.
BEST DUST SUPPRESSION METHODS FOR SCRAP HANDLING
The volume of material the scrap handling industry processes fluctuates with the economic and social climate, but the issue of dust is ever-present. The many properties of scrap materials and the sheer volume of dust requires handlers to examine every step of their material flow, from production to processing, to ensure compliance. Experts at BossTek can perform a full assessment of the material lifecycle and work with operators to implement effective dust suppression methods and create a dust control plan that is compliant and economical.
ELIMINATE DUST FROM SCRAP RECYCLING TODAY!
Talk to a dust control specialist today and put an end to fugitive dust.