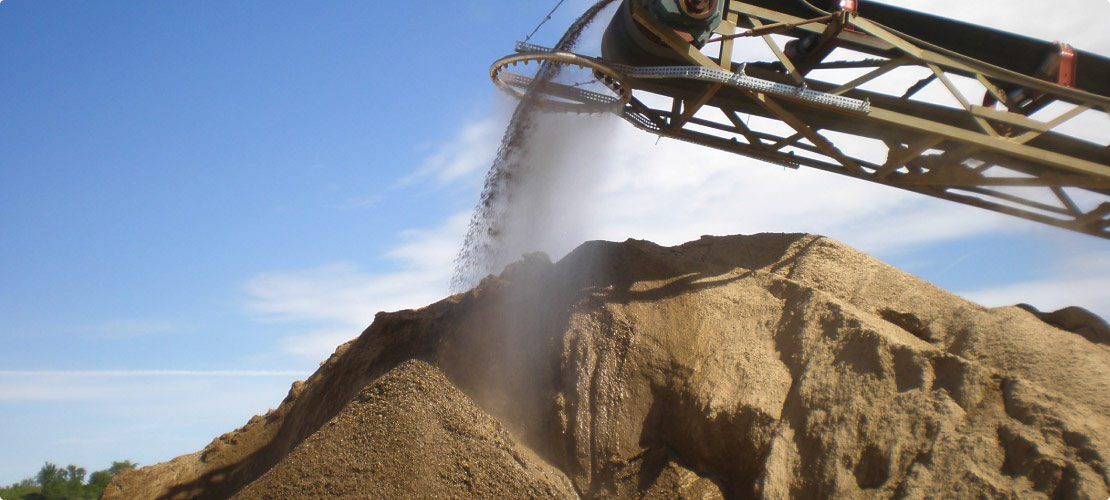
You know you have a conveyor dust problem when you can see it from space. A 61-mile conveyor belt runs from the Moroccan-controlled Bou Craa phosphorus mines in Western Sahara to the coast. Built in 1972, this system conveys 2,000 metric tons of rock per hour to the port city of El-Aaiun. Although the conveyor is covered, prevailing winds from the north still spread dense dust up to a kilometer away and fine particulates several kilometers further.
Figure 1: Bou Craa Conveyor in Northwest Africa. Image courtesy of Google Earth 2023
“The emissions originate from a wide variety of raw and processed materials,” said Michael Kelley, President of BossTek,
“Although the size and mass of the conveyed material play a big role, some types of fugitive emissions like Respirable Crystalline Silica (RCS) come from specific types of substances like limestone and coal, which are more regulated than other particulates.”
Dust has a significant impact on the cost of operation. Low air quality can reduce worker morale and productivity. Dust can clog rolling and mechanical components, increasing labor and downtime for cleanup and maintenance. Ultimately, excessive particulate emissions will result in workplace safety violations and potential downtime if they’re not addressed. This is why risk managers, compliance controllers, and environmental managers are turning to atomized mist as an affordable and versatile conveyor dust control solution.
HOW IS CONVEYOR DUST GENERATED?
Dust is generated by a conveyor in four ways: wind, disruption, transition, and impact.
Wind on outdoor conveyors can be mitigated with coverings, but not completely. Weather conditions are unpredictable and for longer conveyors that are exposed to the elements, there are atomized mist solutions that treat the cargo prior to the long journey. Other conveyors that drop material from high places may require another, more mobile and versatile solution to adjust to changing conditions.
Disruption happens along the conveyor path. Between idlers, the belt slumps slightly, then the trough angle realigns with every new roller. This action causes the cargo to shift and bounce slightly along the belt path, causing dust emissions.
Transition dust happens after the cargo is discharged from the conveyor. When the material encounters the head pulley, it either falls or clings to the belt. As it falls, material not contained by a drop chute separates, exposing the entire stream to ambient air currents allowing emissions. Dust and fines lodged in the belt’s cracks and divots that aren’t discharged (“carryback”) drop along the return belt path, creating emissions that fill the air and pile under the stringer.
Impact emits dust when the discharged material hits the side of the hopper or transfer chute, then happens again when it lands in a vessel, on a pile, or onto another moving conveyor. Depending on the drop height, weight, density, dampness, and the conditions of the landing zone (dry material, the speed of the receiving conveyor, etc.), material impact causes turbulence and shifting leading to airborne emissions.
DIFFERENT CONVEYORS, DIFFERENT DUST SOLUTIONS
Although there is a vast range of conveyor designs unique to every operation, the most common conveyors used in bulk handling are standard conveyors, stacker conveyors, and tripper conveyors.
Standard conveyors are static units that receive material, allow it to settle in an enclosure, then move the cargo at high speeds to another point where it is discharged. There are two good points to address dust, at the point of discharge or in the settling zone. At the point of discharge, misting heads can spray water or a water/surfactant formula onto the discharge stream. In the settling zone, misting heads offer surface suppression on cargo before it leaves the enclosure. The wet shell on the top of the cargo mitigates emissions while travelling down the conveyor path.
Stacker conveyors are tall, inclined belts that can be mobile or static, which receive cargo, move it to a height, then drop it into a vessel or create a pile. The discharge of material is generally long and uncontrolled, so sock chutes and misting rings are used to escort the material to the endpoint without emissions. Stacker conveyors are rarely equipped with elaborate belt cleaning systems, so emissions from carryback are common. Due to the height of the discharge, these emissions can travel long distances, so mobile cannons that can be adjusted for wind conditions are recommended for these conveyors.
Tripper conveyors are constantly moving horizontally on a track system distributing material evenly across a designated area. Tripper conveyors are commonly found in massive enclosures where indoor air quality can become a potential violation. An elaborate return belting system using several pulleys can contribute to dust from carryback. Strategically placed mist cannons for wide-area suppression are recommended for these conveyors.
READY FOR A QUOTE?
Talk to a dust control specialist and get a quick quote for your project.
CONVEYOR AIR QUALITY REGULATIONS
Field tests have shown that atomized mist is one of the best controls of airborne RCS in bulk handling settings. RCS is highly regulated across industries due to its association with chronic and deadly diseases like silicosis, pneumoconiosis, and COPD. This is due to the small size and sharp crystalline shape which damages lungs. Silicon dioxide is formed into a crystalline structure over millions of years. Thirty percent of all minerals are silicates (minerals containing silica), and geologists estimate that they could comprise up to 90 percent of the Earth's crust. [1]
Dust size is measured by width in micrometers or microns (µm) and volume in micrograms (µg) using personal detection devices. Light weight Particulate Matter (PM) as large as 200 µm can remain airborne on ambient air currents and becomes no longer visible to the naked eye under 100 µm. RCS can be the microscopic size of <PM10, meaning the particles avoid the body’s natural defenses and penetrate deep into the lungs.
The Occupational Safety and Health Administration (OSHA) Final Rule for RCS dust emissions in the bulk handling industries sets a personal exposure limit (PEL) of 10 µg (stated as parts per million [ppm]) over a time weighted average (TWA) of 8 hours. [2] For perspective, a single grain of salt is ~58 ug. The TWA compensates for workers moving in and out of different concentrations of RCS throughout a shift, but exposure over that period should be limited.
“The OSHA Final Rule suggested dust control methods are generic, mostly involving surface suppression, ventilation, and the use of chemical surfactants,” said Kelley. “Regulators are testing for minuscule concentrations in the air, so 100% prevention is the goal, but in most high-volume industrial bulk handling environments that’s just not possible.”
WHY IS ATOMIZED MIST EFFECTIVE FOR CONVEYORS
Research has shown that droplet sizes need to be roughly the same size as the airborne particulates to be effective. Water remains the sole medium for control of airborne outdoor emissions. Hoses and sprinklers create droplets between 200 µm and 1000 µm compared to atomized mist, which is sized in the range of 15 µm to 200 µm. Droplet sizes greater than 200 µm are only adequate for wetting surfaces, but don’t offer airborne dust suppression. This is due to the slipstream effect.
Atomized mist is effective because the fine engineered mist is distributed using a powerful fan-driven cannon design or strategically-placed misting bar or ring. Nucleating nozzles fracture pressurized water into millions of tiny droplets between 15 μm and 200 μm in size, preferably applied at the point of emission. As a droplet moves through the air, the mass creates a strong current that moves around it called the slipstream effect. Particles get caught in the slipstream and remain unaffected. In some cases, the droplet can even lift the smallest particles, making the issue worse. Atomized droplets, on the other hand, travel with the particles, collide with them, and drag them to the ground.
The tiny droplets raise the humidity of the target area, float on atmospheric air currents with dust, and capture particles. Settling droplets provide surface suppression evenly across the material using less water, drastically lowering the volume of runoff and reducing the chance of pooling.
DOSING SURFACTANTS FOR CONVEYOR DUST CONTROL
Surfactants are a category of chemical additive that is distributed by dust cannon or atomized misting system, particularly helpful for the suppression of dust emitted by naturally hydrophobic materials (shale, coal, etc.). Materials are hydrophobic when the interaction between the water molecule and the material is negative, causing the water molecules to bond to themselves rather than the material. This creates beaded droplets that roll off the surface rather than wet it, like on a water-resistant jacket. Surfactants promote ionic bonds that spread the droplet across the material, allowing hydrophobic materials to cling and cake.
This is particularly beneficial during transport and transfer of dusty cargo. When surfactants are dosed into water prior to applying it to the material, the chemical is evenly distributed so dust particles stay within the cargo stream rather than becoming airborne. Dosing pumps allow operators to control the volume of chemicals. A specialized dust cannon like the DustBoss® DB-30 Injektor™ is excellent for stockpile and storage barn dust management. However, most atomized misting heads, rings, and cannons can be fitted with dosing pumps.
MISTING EQUIPMENT FOR CONVEYORS
Mist cannons use a high-powered fan at the back of a cone-shaped barrel. Mounted on the front exit-side of the barrel is a ring manifold with multiple nozzles that fracture pressurized water into atomized droplets. Air is forced through the barrel to propel millions of minuscule droplets into the air. Misting heads use water pressure to fracture the water with similar nozzles and spray the fine mist with precision in a limited space.
- DB-M Mini - Discharged material at conveyor transfer points will separate, offering an excellent opportunity to introduce moisture from strategically placed misting heads. The Mini is a directional misting head. This option can be accompanied by a dosing system to introduce dust suppressing surfactants to mitigate downstream dust emissions.
- DB-Ring - Material that is discharged from a conveyor and not contained in a transfer chute is exposed to ambient air currents. By using a stainless-steel ring, the material flow is surrounded by a curtain of light mist that falls with the material preventing fugitive emissions from traveling.
- DB-10 – The compact mist cannon is mounted on two wheels with a tall handle, similar in size to a snow blower. It’s light and easy to maneuver, while still offering industrial-sized dust control up to 30 ft (10 m) at a 20° throw angle.
- DB-30 – Often mounted in high points above material in coal barns, cement domes, and other large indoor facilities that utilize conveyors, this cannon has a cone reach of 100 ft (30 m) and a coverage area of up to 2,880 m2 (31,000 sq ft) when equipped with oscillation.
- DB-60 - Popular with storage facilities that need a mobile solution to move with wind and pile rotation, it has a 200 ft (60 m) throw distance and covers up to 125,000 sq ft (11,612 sq m) when equipped with oscillation.
PREVENTING CONVEYOR DUST
When conveyor dust is emitted, it doesn’t stay contained to the immediate area but can spread across the operation and past the site line into neighboring operations. As we can see from Bou Craa, sometimes emissions can travel for miles. Community complaints about dust emissions from normal conveyor operations can spark inspections, violations, fines, and sometimes forced downtime until the problem is adequately addressed.
“There have been too many instances where we’re contacted by frantic operators trying to get dust control solutions to their sites, so they can quickly get production back up following a regulatory violation that has temporarily shut them down,” said Kelley,
“We do our best to fulfill those requests, but we recommend a proactive approach. We can schedule a visit and provide expert advice with economical solutions.”
For an assessment of how BossTek® can control dust, reduce downtime, and improve environmental compliance. Contact Us today!
REDUCE CONVEYOR DUST AND IMPROVE AIR QUALITY TODAY!
Receive a FREE site assessment and talk to a specialist today about conveyor dust control.