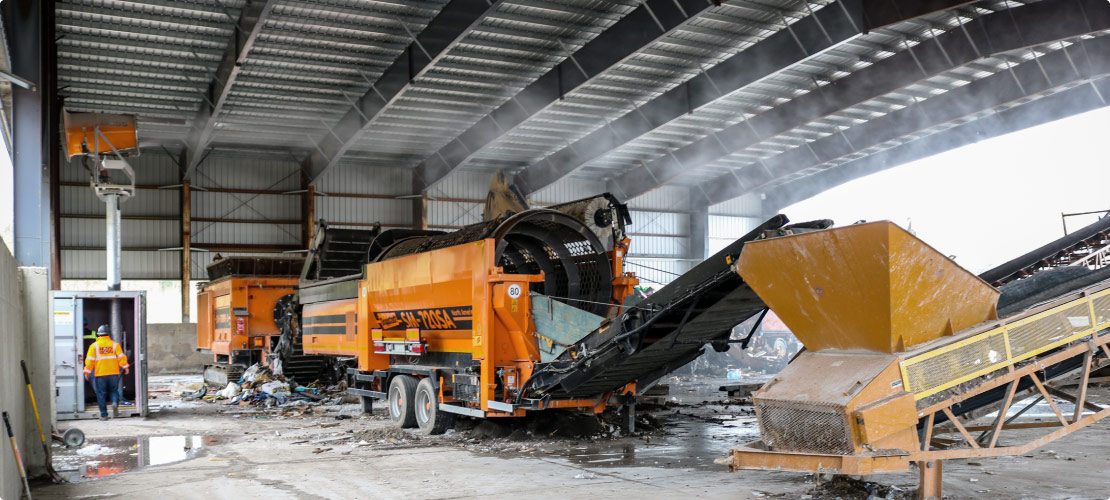
Many bulk handling industries enclose their operations to avoid emissions leaving the site line and drawing complaints from neighbors. When a company does this, it then turns its attention to indoor dust suppression to protect workers.
Some enclosed operations like recycling and MSW intake centers have several points of emission. Other indoor activities like demolition and manufacturing goods from raw materials like wood, metal, stone, etc., require directed suppression of potentially harmful emissions at the source. The list of bulk handling applications that need indoor dust control is extensive, from cement domes, coal barns, mining, tunneling, and raw material processing operations.
What all these industries have in common is people working in the area where the dust is produced. Beyond making the area dirty and unpleasant to be in, excessive dust presents a regulated workplace hazard. There are many ways to approach the suppression of indoor dust emissions, but more and more, environmental managers, risk managers, and compliance officers are turning to indoor atomized mist technology as the standard method of dust control for its versatility and effectiveness.
SOURCES OF INDOOR DUST
The Clean Air Act categorizes the sources of dust by major sources and area sources. It says, “Major Sources are defined as a stationary source or group of stationary sources that emit or have the potential to emit 10 tons per year or more of a hazardous air pollutant or 25 tons per year or more of a combination of hazardous air pollutants. Area Sources are any stationary sources that are not a Major Source.” [1]
SOME EXAMPLES OF MAJOR AND AREA SOURCES ARE:
- Indoor demolition dust has the potential of emitting toxic or highly regulated particulates from asbestos, drywall, and insulation. As mini excavators, mini front loaders, and jackhammers remove walls, tiles, metal, wood, and glass, and then sorts debris into piles, the dust can be so dense that it quickly fouls air intakes, causing downtime and reducing equipment life.
- Indoor recycling plant dust is a problem that can affect workers throughout their shifts. The vibration screening process separates certain materials, but at some point, humans need to stand at a conveyor, identify materials, and sequester them into bins. Although PPE helps protect workers from emissions, detectable ambient concentrations of dust may still yield violations unless controlled.
- Tunneling dust is an issue because ventilation may be limited. Once the boring machine has made its pass, mini excavators and drilling rigs must create maintenance and escape shafts from each tunnel. This can produce localized dust which, unless suppressed at the point of emission, travels down the tunnel with ambient air currents in high concentrations.
- Indoor bulk handling dust has the potential of creating tons of emissions per year. Front loaders, tripper conveyors, and stacker conveyors are constantly dropping new cargo, disrupting stored material, and producing emissions. Although operators may remain in sealed cabs for much of their shift, maintenance staff, cleaning crews, and other personnel can be exposed to a dangerous volume of emissions, particularly highly regulated respirable crystalline silica (RCS). Moreover, conveyor rolling components and machine parts are also easily fouled and may cause excessive downtime and maintenance.
- Indoor crusher dust can be quite prevalent in mines and quarries. Sometimes housed in the mine or in processing plants, the reduction of large rocks and boulders into aggregate or smaller can produce an inordinate volume of emissions, particularly RCS. Addressing these airborne particulates at the point of emission is key to controlling indoor air quality (IAQ).
MEASURING INDOOR DUST EMISSIONS
There are many scenarios where workers get exposed to dust emissions. Often these emissions are invisible to the naked eye, and the smaller they are the more dangerous and regulated they are. Workplace safety inspectors from the Environmental Protection Agency (EPA) or Occupational Safety and Health Administration (OSHA) have been known to test indoor operations for IAQ if they suspect excessive emissions. [2]
Investigators measure dust size by width in micrometers or microns (µm) and volume in micrograms (µg) using personal detection devices. Light weight Particulate Matter (PM) as large as 200 µm – roughly the size of a grain of sand -- can remain airborne on normal ambient air currents and is no longer visible to the naked eye under 100 µm. At the size of <PM10 (the IAQ regulated size threshold for most airborne particles), the dust avoids the body’s natural defenses and penetrates deep into the lungs.
INDOOR DUST REGULATIONS
To be effective, droplet sizes need to be roughly the same size as the airborne particulates. In the past, the use of hoses and sprinklers was not appropriate for indoor applications since they create droplets between 200µm and 1000µm. These would saturate the area, creating pooling, which introduces slip and fall hazards, another common OSHA violation.
Droplet sizes greater than 200µm don’t offer airborne dust suppression due to the slipstream effect. Atomized mist, on the other hand, produces droplets in the range of 15µm to 200µm, small enough to collide with airborne particulates and pull them to the ground. There is little to no pooling and with proper indoor ventilation, the droplets follow the dust and are absorbed by the emission.
The human health effects of PM are well-established and are used to set the National Ambient Air Quality Standards (NAAQS).[3] There are two types of ambient air quality standards identified by the Clean Air Act, primary and secondary. Primary standards provide public health protection to "sensitive" populations (asthmatics, COPD, children, seniors, etc.). Secondary standards provide public welfare protection (animals, crops, vegetation, and buildings).
METHODS OF INDOOR DUST CONTROL
- PPE – Respirators filter particulates very effectively if worn correctly. Workplace safety managers often have difficulty ensuring masks are properly worn, filters are swapped out on schedule, and masks are worn when supervisors aren’t watching. This is particularly true when invisible PM10 & PM5 are present.
- HVAC filtration – Dust is drawn toward a duct system, leading to a filtration and collection hub. Dust passes through filtration media, then a shot of pressurized air from an air tank is passed through the media to extract dust into a collector funnel in the bottom where it is captured in a receptacle. This system is only effective if placed directly above a static dust emission point. Energy costs to run high-powered vacuum pumps can be excessive. Ductwork and filtration systems need regular maintenance from dust buildup, and the air tank can burden the compressed air system, raising the cost of operation considerably.
- Natural ventilation – Traditional architectural designs with upper windows and/or rooftop ventilation have historically been effective in drawing dust upward toward a ceiling and out of the openings. However, there are several issues with this method, the most prevalent being that it doesn’t stop the dust from being airborne indoors and then exhausts particulates to the outdoors where it can leave the site line. This leads to both indoor and outdoor violations. The effectiveness of this method is dependent on the wind outside making the Bernoulli principle possible to create a strong enough air current. [4]
- Atomized Mist Spray Heads – Set above static dust generation points like crusher feeders, conveyor discharge points, and screen vibrators, spray heads create a fine atomized mist that suppresses dust at the immediate point of emission.
- Indoor Dust Cannons – Many industrial dust control cannons on the market are too powerful for indoor applications. That’s why BossTek® designed some smaller units that can raise the humidity of an area or easily be wheeled and pointed at an area of operation for a more directed approach. They combine the effectiveness of atomized mist with the added benefit of directed air circulation for indoor dust suppression.
READY FOR A QUOTE?
Talk to a dust control specialist and get a quick quote for your project.
TYPES OF INDOOR MISTING CANNONS
An automated indoor misting cannon has a high-powered fan at the back of a cone-shaped barrel. Mounted on the front exit side of the barrel is a ring manifold with multiple nozzles that fracture pressurized water into microdroplets roughly the same size as the airborne dust. The fan creates a powerful air stream that is concentrated in the barrel, directing the air at a high velocity out the front. Once it encounters the misting ring at the front, the air carries millions of microdroplets and distributes them in a dust suppressive plume wherever the cannon is pointed.
Indoor misting cannons can be set in specific locations throughout the operation and managed by remote control. The units are automated, so after being turned on, workers can leave to perform other tasks. This reduces labor and worker exposure to hazardous IAQ.
DustBoss® DB-10 – Compact and mounted on a push carriage small enough for one person to maneuver and set up. A ¾ HP fan delivers 3335 CFM (94.43 CMM) of airflow, powered by 120-volt current, and is about as loud as a hand-held hair dryer. The circular manifold has 12 atomizing nozzles that fracture pressurized water into a fine mist. The unit creates a fog in a cone up to 30 feet (10 meters). Using the 0-50º vertical adjustment, the cone can be directed at specific emission zones. It is offered with a standard wheeled carriage but can be specified with alternate mounting as needed.
DustBoss® DB-30 – The DB-30 has a more traditional industrial dust cannon configuration with 0-70º of oscillation and double the throw distance of the DB-10. Equipped with 30 brass nozzles, it produces a throw of more than 100 feet (30 meters), covering an area of 6,100 square feet (566 square meters). The premium-efficiency, direct drive fan motor delivers 9,200 CFM (260.5 CMM) of airflow.
TYPES OF INDOOR DUST CONTROL SPRAYERS
Sprayers use pressurized water rather than fans to distribute droplets. Fracturing the pressurized water with specialized nozzles causes the spray to become a fine mist that provides even distribution across an area with less pooling and runoff than standard hoses or sprinklers. What pressurized spray allows is farther reach distances and more precision.
DustBoss® Atom™ - The Atom uses a pump powered by a 9.1 HP diesel engine to throw mist 30 meters (~100 feet). The unit’s 0-65º vertical adjustment and 100º oscillation range increase the coverage area to 567 sq/m (6,100 sq/ft). Using the hand-held remote control, operators can set the oscillation range from the cab of their rig or at a safe distance from the demolition zone.
DustBoss® DB-M Mini – The DB-M Mini is a static misting head that directs spray onto a cargo stream, stopping dust from becoming airborne. As pressurized water is pumped through the atomizing nozzles, the head evenly distributes dust controlling droplets that suppress emissions without saturating the material.
THE COST OF INDUSTRIAL INDOOR DUST CONTROL
There are direct costs and indirect costs of indoor dust. Direct costs are what is spent to mitigate the direct results of dust emissions. This includes the cost of labor for cleanup of the area, maintenance on mechanical components, the expense of replacement parts (seized conveyor rollers, filters for intakes, PPE, etc.), and fines from violations. Indirect costs are less tangible and often happen much later as a result of dust. Examples are settlements of lawsuits from workplace injury claims, greater insurance premiums, forced downtime from violations, and lower morale/higher turnover due to an unhealthy and unpleasant work environment.
PLANNING FOR INDUSTRIAL INDOOR DUST SUPPRESSION
Our dust control specialists will review your indoor operation and make recommendations that best suit your needs and budget. This review starts at emission points and ways to prevent dust. Sometimes direct spray onto material is required using spray heads prior to or at the point of discharge. Other times cannons can be affixed at high points of the facility, using oscillation to keep emissions from traveling throughout the enclosed facility.
By reviewing your options, then installing the proper indoor dust mitigation technology, managers can reduce the amount of labor for cleanup and maintenance, improve workplace safety, and lower the cost of operation.
Contact us today to get an assessment of your operation!
GET A QUOTE FOR INDOOR DUST CONTROL TODAY!
Receive a FREE quote and talk to a dust control specialist today to end fugitive dust!