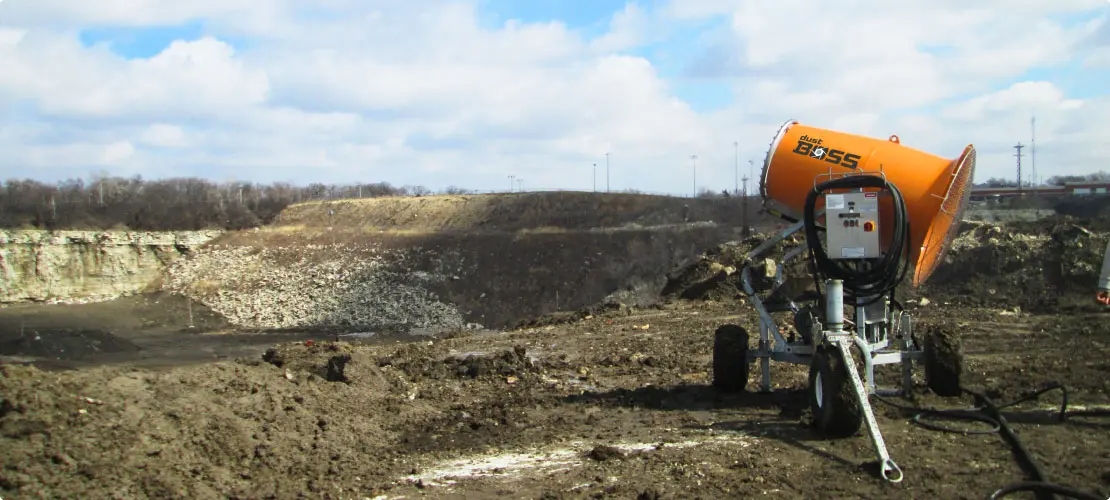
Dust is the general name for minute solid particles of a diameter of less than 500 micrometers. In construction, demolition, and renovation situations, dust of differing sources poses a serious and recognized health risk to workers causing acute and chronic diseases such as silicosis, sarcoidosis, asbestosis, coal miner's pneumoconiosis, and other pneumoconiosis type ailments. In addition to the health risk, dust emissions also pose a threat with its ability in some sectors to be flammable.
Dust in generated from a very wide range of activities both industrially and domestically. Activities such as mining, construction, and agriculture are industries that are large contributors to general atmospheric dust levels. Dust exposure is dependent on the amount of dust emitted, which depends on the physical characteristics of the material and the methods of handling of the material. Dust exposure generally occurs from, but is not limited to, being exposed to dust from one or more of the following tasks:
- Abrasive blasting involving harmful materials.
- Demolition of concrete and masonry structures.
- Through the breaking of ore.
- Through release of previously generated dust through processes such as loading and dumping of materials.
Implementing new dust control methods for industrial sites is essential to protecting workers from various dust generating tasks.
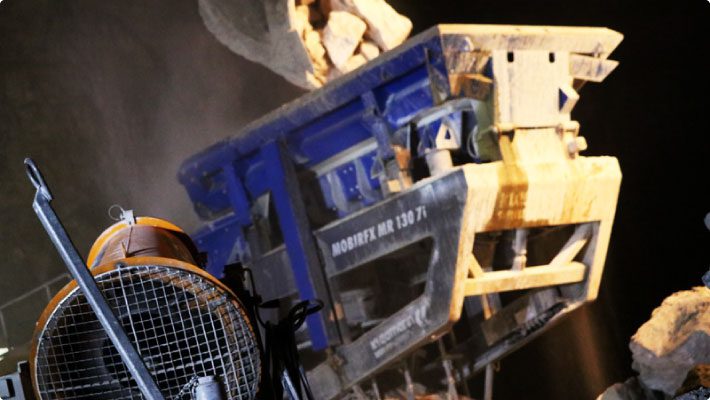
Preventing harmful mining dust emissions with dust control systems.
FUGITIVE DUST AND THE NEED FOR DUST CONTROL
Dust is produced in a very wide range of sizes. Larger, heavier particles tend to settle out of the air and onto a surface and smaller, lighter particles have a tendency to hang indefinitely in the air.
There are two main types of dust that exist on a worksite. First of all, there is fibrogenic dust. Fibrogenic dust is so named because it is a kind of dust that has fiber like tendencies. Fibrogenic dust is biologically toxic and if retained in the lungs can impair the lungs' ability to function properly. Examples of this kind of dust include asbestos dust and free crystalline silica. Secondly, there is the category of inert dust, which is defined to be any dust containing less than 1% of quartz content. Typically, any health effects caused by inert dust are potentially reversible, as opposed to the fibrogenic dust's more permanent effects. However, inert dust has the potential to obscure visibility, cause unpleasant deposits in exposed bodily orifices, and potentially injure mucous membranes or the skin with some sort of chemical action.
For occupational health purposes, dust is classified by its size into the three categories of respirable dust, inhalable dust, and total dust. Respirable dust is the kind of dust that is small enough to penetrate deep into the lungs and bypassing the nose, throat, and upper respiratory tract. It is defined as being of a size of less than or equal to 5µm, which is about 1/12th the width of the average human hair. Inhalable dust is dust of a median size of 10 µm that is trapped in the nose, throat, and upper respiratory tract. Total dust includes all airborne particles, without regard to size or composition.
Dust control is necessary due to both health hazards and industrial problems. Excessive dust emissions can cause such health issues as occupational respiratory diseases; eye, nose, and throat irritation; and skin irritation. In addition, dust is an industrial problem. With its potential risk of dust explosions and fires, it can potentially damage worksite equipment, it impairs visibility, it can cause unpleasant odors, and it is a potential problem in community relations.
As far as health hazards to workers, this occurs when workers are exposed to excessive amounts of harmful dusts. The harmfulness is dependant on the composition of the dust (i.e. chemical or mineralogical), the concentration of the dust (either by weight or quantity of dust particles), the size and shape of the particle (i.e. fibrous or spherical), and lastly, the exposure time.
The biggest concern of people exposed to worksite dust is that long-term exposure to certain harmful respirable dusts can cause a condition known as pneumoconiosis. Pneumoconiosis is a respiratory disease which is categorized by the tissue response due to the buildup of mineral and/or metallic dust particles in the lungs. Pneumoconiosis is a general name for specialized types of dust-related lung disease.
Of particular note as far as pneumoconiosis goes, there are three varieties that are much more prominent and common in industrial situations. First of all is silicosis, which is a chronic, irreversible disease which results in shortness of breath due to scarring of the lung tissue. Crystalline silica is naturally present in the following materials used in construction:
Many abrasives used for blasting.
- Brick, refractory brick
- Concrete, concrete block, cement, mortar
- Granite, sandstone, quartzite, slate
- Gunite
- Mineral deposits
- Rock and stone
- Sand, fill dirt, top soil
- Asphalt containing rock or stone
Secondly, there is the form of pneumoconiosis known commonly as black lung, but whose official name is coal worker's pneumonia (CWP). In this disease, respirable dust particles from coal mining and/or refining collect in the lungs and darken the tissue, causing breathing difficulties.
Thirdly, there is the form of pneumoconiosis called asbestosis, which is caused by asbestos fibers. This is an irreversible disease that causes shortness of breath and an increased risk of cancer, including a very rare type of cancer known as mesothelioma. Typical exposure occurs in mining and demolition sites.
See how dust control cannons help with silica compliance!
HAZARDOUS SLAG DUST
Slag is the name for the nonmetallic byproduct that occurs from the production of iron. Typical slag is composed of between 30-50% by weight of calcium oxide, 0-20% by weight of magnesium oxide, and less than 1% by weight of crystalline silica. Slag contains trace amounts of such chemicals as manganese oxide, titanium oxide, chromium compounds, sulfur compounds. Exposure to slag dust can cause varied reactions including eye irritation, dermatitis, acute inhalation effects, and chronic inhalation effects.
Airborne slag dust has the potential to cause immediate or delayed irritation or inflammation of the eyes. Any eye exposure to large amounts of dry powder or wet slag requires immediate first aid in order to prevent significant and permanent damage to the eye.
Slag is capable of causing different skin reactions including dry skin, discomfort, irritation, and dermatitis. The dermatitis reaction can be caused by either irritation or allergies. In the case of irritant dermatitis, this is caused by the innate physical properties of the slag, i.e. moisture and abrasion. The allergic contact dermatitis however is typically caused by a sensitivity due to the presence of hexavalent chromium in slag. This reaction can range from mild skin irritation and rash to the presence of severe skin ulcers. Persons already sensitized may react upon the first contact with slag; however, it is also possible that a person may develop an allergy to the substance after repeat exposure to the slag.
In the case of acute inhalation effects, the slag dust has the potential to cause nose, throat, and lung irritation, including choking. The level of irritation is related to the degree of exposure of the individual.
Chronic slag dust effects are also dependent on duration and degree of exposure to the slag dust over time. The lung disease silicosis is a threat to exposed individuals as slag does contain crystalline silica. It is also possible that slag dust has a carcinogenic effect due to the presence of both the crystalline silica and the hexavalent chromium in the slag. These two substances are classified by both the IARC and the NTP as known human carcinogens. In addition, some studies have shown that repeat exposure to respirable silica, even without the presence of silicosis, could be associated with an increased risk of the incidence of autoimmune diseases including scleroderma, systemic lupus erythematosus, rheumatoid arthritis, and some disorders involving kidney function. Silicosis also increases the risk of tuberculosis in persons affected with the disorder. Finally, it has also been shown that there can exist an increased risk of chronic kidney disease and end-stage renal disease in workers who had exposure to respirable crystalline silica.
READY FOR A QUOTE?
Talk to a dust control specialist and get a quick quote for your project.
DUST CONTROL METHODS
Pyramid Approach
The Pyramid Approach consists of three different methods of controlling dust: Collection, Containment, and Suppression. Any one of these can be used as well as a combination of these methods. The choice of method varies, based on budget, desired level of effectiveness, and structural constraints.
Dust Collection
A dust collection system works through ventilation principles to carry a dust-filled air stream through some ductwork to where it is then collected and isolated. A dust collection system relies on four main components in order to effectively capture and collect the dust. These four main components consist of an exhaust hood to capture dust emissions at their source, a system of ducts in order to transport the captured dust to the dust collector, a dust collector in which to store the removed dust, and a fan and motor system in order to provide the required suction for the system. Attention must be paid to the selection and implementation of all four of these components as poor performance of one component will adversely affect the whole system
Dust collection system sketch.
The dust collection method relies on using the principle of creating a pressure differential between two points in order to create a corresponding airflow that in turn, brings the dust into a more desirable location. That is to say that the use of a suction fan on one end of some ductworks creates a low pressure zone as opposed to the now relatively higher pressure zone in the dusty area. Like water flowing from a high point to a low point on a mountain, the air now flows from the high pressure point to the low pressure point. In actuality, a few different types of pressures are exerted by the airstream that need to be taken into account by the designer of the dust collection method system. In addition, the airflow and peculiarities that arise when an airstream enters a ventilation hood, turns down corridors, and bounces off of walls of the ventilation ducts must considered as well in all design of a dust collection method system.
Structural Containment
Dust control can be accomplished by simply enclosing the dusty area inside a structure. Sides and sometimes the top of the structure must be closed to accomplish complete dust control. This method is a permanent solution. Enclosures are expensive to both build and to maintain. Each site is unique and determines the size and location of the structure.
Wet Dust Suppression
There are two different types of wet dust suppressions: one wets the dust before it is airborne (surface wetting) and the other wets the dust after it becomes airborne. It is also important to be aware of the fact that it should not be automatically assumed that by 'wet', it means solely water is being used in this process. In many cases surfactants or chemical foams are often added to the water into these systems in order to improve performance. A water spray with surfactant means that a surfactant has been added to the water in order to lower the surface tension of the water droplets and allow these droplets to spread further over the material and also to allow deeper penetration into the material. A chemical foam is generally water and some sort of special blend of surfactant. A foam allows the surface area per unit volume of wetted material to be increased, which thereby increased the efficiency of the wetting. These products all have their plusses and minuses in being used, most of which generally come down to cost of the wetting material, efficacy of the wetting material, and potential environmental and product contamination by the wetting material.
Surface Wetting
The principle behind surface wetting is the idea that dust will not even be given a chance to form and become airborne. With this method, effective wetting of the material can take place by static spreading (wetting material while it is stationary) and dynamic spreading (wetting material while it is moving). For static wetting, more effective dust suppression arises by increasing the surface coverage by either reducing the droplet diameter or its contact angle. For dynamic spreading, more factors come into play such as the surface tension of the liquid, the droplet diameter, the size of the material being suppressed, and the droplet impact velocity.
Airborne Dust Capture Systems
Airborne dust wet suppression systems work on the principle of spraying very small water droplets into airborne dust. When the small droplets collide with the airborne dust particles, they stick to each other and fall out of the air to the ground. This collision between the particles occurs due to three factors involving both the water and the dust particles. As a dust particle and water particle approach each other, the airflow could move the particle around the droplet, have a direct hit on the droplet, or barely graze the droplet. It is this factor that leads us to the second factor, which is that droplets and particles that are of similar sizes have the best chance of a collision. This is what we call the "slipstream effect". If a droplet is smaller than the dust particle or vice versa, then they may never collide and instead just be swept around each other. The last factor is the dependence of an electrostatic force on a droplet and how the path is affected by this force. Just like with magnets, similarly charged particles repel each other. Thus it is advantageous to have the particles either both neutrally charged (so that they neither repel nor attract one another) or oppositely charged (so that they attract one another) in order to increase the likelihood of a water and particle collision.
See how atomized mist avoids the slipstream effect!
The problem with airborne matter includes a broad range of industries and that most airborne dust particles occupy the size range of between .5 and 100 microns. Coal dust and fly ash range from about 1 to 10 microns. Some particles are within the size range of bacteria, which is .5 ato 50 microns. Paint pigments are even smaller. The U.S.B.M. defines particles between 1 and 10 microns as "respirable dust". Larger particles do not reach the lungs, and smaller ones mostly go "in and out".
How Big is a Micron?
We are trying to control microscopic particles which must involve the use of some medium that can also be broken down to microscopic - like water. This explains why water "sprays" are not very effective on respirable dust: typical droplet sizes are 200 to 600 microns - much greater than the respirable dust, which is less than 5 microns. Thus, water sprays can be improved by designing nozzles which produce smaller droplets. Dust suppression is acquired by water particles that capture the dust particles and the weight of the dust. Water molecules agglomerate the dust and gravity brings it to the ground.
The airborne dust wet suppression systems can be organized into more or less two broad groups of either being a finely atomized water spray or an electrically charged fog. A finely atomized water spray device is typically used on a smaller site with limited air turbulence or when the velocity of how the dust disperses is less than 200ft/min.
Micron Sizing Diagram
Finely Atomized Water Sprays
Finely atomized water sprays are normally used at transfer points without excessive turbulence or when the velocity of dust dispersion is less than 200 ft/min. The optimum droplet size, water usage, relative velocity, and number and location of nozzles depend on the conditions at individual transfer points.
Electrostatically Charged Fogs
Electrostatically charged fog uses charged water droplets to attract dust particles, which increases collision. The atomized water droplets are charged by induction or direct charging.
Design of a Water Spray System
The most integral part of a water spray system is of course the nozzle. The nozzle's physical characteristics affect such factors as droplet size, droplet distribution, droplet velocity, spray pattern of the droplets, angle of the droplets, water flow rate, and water pressure.
The spray nozzle is the heart of a water-spray system. Therefore, the physical characteristics of the spray are critical. Factors such as droplet size distribution and velocity, spray pattern and angle, and water flow rate and pressure all vary depending on the nozzle selected. In general, a fogging type nozzle producing droplets of a size of 10-150µm is used for an airborne dust control system and a flat-spray nozzle producing coarse droplets of a size of 200-500µm at high pressure is used for a surface wetting situation. Typically, higher droplet velocity is desirable for both types of dust controls through water sprays as this allows for more dust particles at a time to be suppressed. The spray angle is necessary to know because it determines the amount of coverage that a certain nozzle with give and thus will let one know how many nozzles are necessary for a given amount of desired coverage area.
REFERENCES
Information for this blog was taken from the following sources:
Bureau of Mines: Mines: U.S. Department of the Interior. Dust Control Handbook for Minerals Processing. Authored by Vinit Mody and Raj Jakhete, 1987.
Center for Applied Energy Research. Environmental and Coal Technologies Research
LaFarge North America. Material Data Safety Sheet: Slag
New Jersey Department of Health and Senior Services Occupational Health Surveillance Program. Stop Silicosis in Sandblasters: Use Silica Substitutes
Occupational Health and Safety Administration. Secondary Lead Smelter
North Carolina Department of Environmental and Natural Resources: Division of Pollution Prevention and Environmental Assistance. Primary Metals
This blog post was originally posted in October 2013 and has been updated in 2019.
IMPLEMENT DUST CONTROL AT YOUR JOB SITE!
Receive a FREE quote and talk to a dust control specialist today to stop fugitive dust!