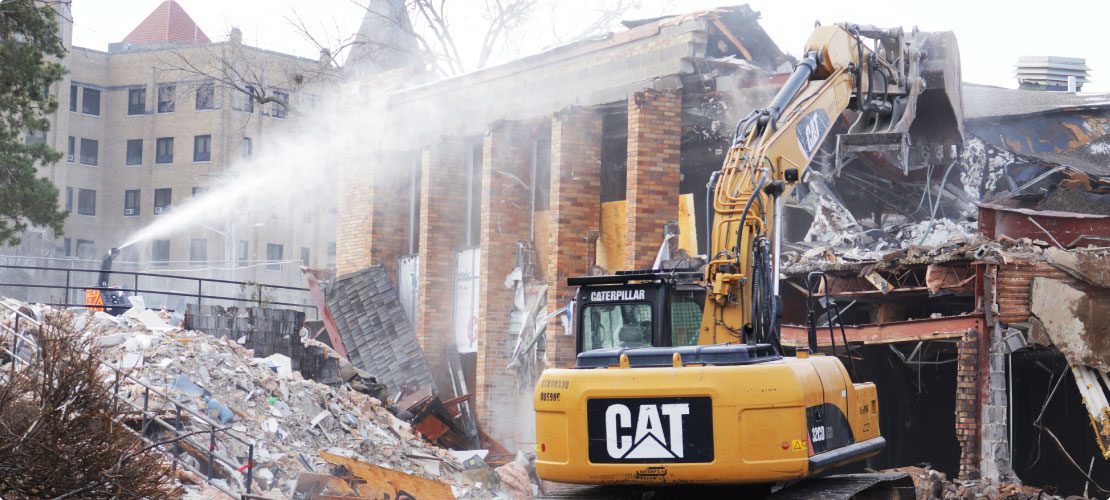
In a survey of owners responsible for facility construction and maintenance, the Construction Management Association of America (CMAA) outlined a set of seven challenges likely to cause construction markets to change direction in the near future. First on the list was the observation that “Aging infrastructure in nearly every market segment is at or beyond its current useful life… represent(ing) trillions of dollars in necessary spending over the next 10 to 20 years to upgrade and replace these assets.”[1]
The statement could be made about many developed nations, and as the built infrastructure in Europe and the U.S. continues to age, demolition and reconstruction firms are likely to see a growing number of business opportunities. At the same time, contractors and engineers are facing a complex set of challenges, some of which have not been a major concern on outdoor projects until recent years.
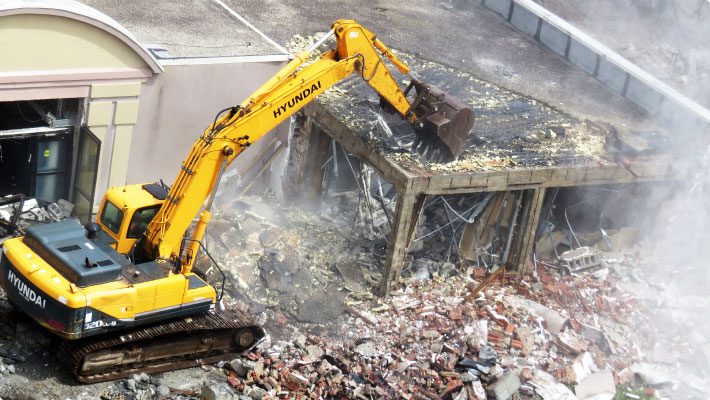
One such challenge is the hazard posed by dust that arises during demolition and debris recycling. In the past, these airborne particles have been treated largely as a nuisance, causing more of an inconvenience than a health or environmental risk. The fact is, the hazards posed by stone and concrete dust in construction applications were detailed more than half a century ago by Marion Trice, an industrial hygienist for the state of North Carolina.[2] And Trice wasn’t the first to recognize the problems. As far back as 1700, Bernardino Ramazzini talked about dust that “would gradually prove fatal to stonecutters who took no precautions” in De Morbis Artificum Diatriba (Diseases of Workers).[3]
Dust is a generic term for minute solid particles, typically less than 500 microns in diameter. In construction and demolition projects, dust particles are created in a wide range of sizes. Larger, heavier particles tend to settle out of the air, while smaller, lighter solids may hang indefinitely. For occupational health purposes, airborne solids are categorized by size as either respirable or inhalable. Respirable dust is small enough to penetrate deep into the lungs, usually identified as particles under 10 microns in size (PM-10). These tiny solids that migrate far into the respiratory system are generally beyond the body’s natural cleaning mechanisms such as cilia and mucous membranes, and are likely to be retained. In contrast, the larger particles in the inhalable dust classification are typically trapped in the nose, throat or upper respiratory tract. To put that in perspective, a human hair typically ranges from 50-75 microns in diameter, illustrating that the most hazardous dust particles in most situations are the ones too small to see.
Other than crushing operations, which must be properly registered and equipped with some form of dust suppression at the material entrance and exit, there is currently not much legislation in the U.K. that specifically addresses dust control in outdoor construction applications.
The issue has taken on increased importance for regulating bodies in the U.S.; however, many contracts in both regions now require dust control. On some projects (such as work for many state DOTs), dust suppression is a mandatory component of all planning and execution, subject to inspection. In both European and U.S. markets, contractors aiming to protect the health of employees and surrounding communities, while preserving the environment and reducing potential liability, would be well served to consider dust suppression a priority in urban and suburban locations. Demolition firms seeking to differentiate themselves from the competition and reinforce a positive environmental image will be likely to view the challenge as an opportunity.
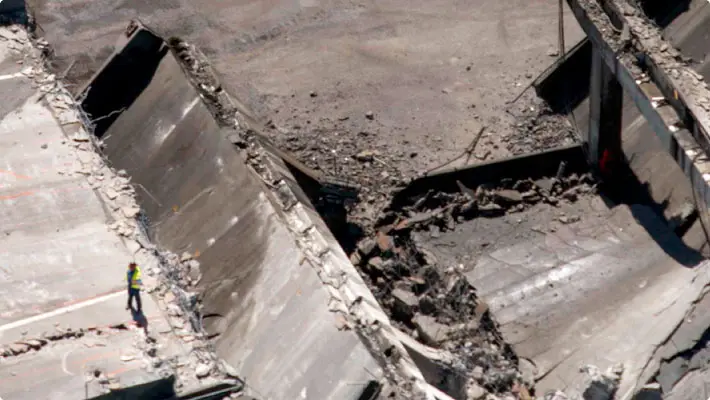
WHAT ARE THE HAZARDS?
As the developed infrastructure in Europe and the United States continue to age, contractors find themselves working in more densely populated areas, with greater risk of public exposure to dust and less open space to dissipate airborne particulates. Some of the problems are fairly obvious. Dust inhaled by workers or members of the surrounding community can irritate airways and exacerbate conditions such as asthma. From a purely financial perspective, when equipment air intake includes significant amounts of dust, it can lead to more frequent maintenance and greater engine wear, causing operating costs to rise. Jobsite dust can also generate complaints from local residents and businesses, affecting community relations and potentially creating obstacles to future operating permits.[4]
A lesser-known hazard associated with airborne dust from deconstruction of older structures is histoplasmosis, an infectious disease caused by inhaling the spores of a fungus commonly found in bird droppings and bat excrement. When liberated by demolition or excavation work, the fungus primarily affects the lungs, though its symptoms vary greatly. The disease can appear as a mild, flu-like respiratory illness, often with a combination of symptoms that can include general malaise, fever, chest pain, cough, headache, loss of appetite, shortness of breath, joint and muscle pains, chills, and hoarseness. Histoplasmosis is not contagious, and cannot be transmitted from an infected person or animal to someone else.[5]
Chronic lung disease from histoplasmosis resembles tuberculosis, and the disease can worsen over months or years. The most severe form involves spreading of the fungus to other organs outside the lungs. Disseminated histoplasmosis is fatal if untreated, but death can also occur in some patients even when medical treatment is received. People with weakened immune systems are at the greatest risk for developing severe and disseminated histoplasmosis, as well as young children and individuals receiving cancer chemotherapy, high-dose/long-term steroid therapy or other immuno-suppressive drugs. The majority of infected adults have no long-term ill effects, or they experience symptoms so mild that they do not seek medical attention and may not even realize that histoplasmosis was the cause.[6]
READY FOR A QUOTE?
Talk to a dust control specialist and get a quick quote for your project.
SILICOSIS
A far greater concern to workers and local communities is the risk of exposure to crystalline silica contained in airborne dust. The term “silica” is a generic reference to the mineral compound silicon dioxide (SiO2), which can be found in either amorphous or crystalline form. Crystalline silica is significantly more hazardous, cited as a cause of the disabling and irreversible lung condition known as silicosis, one of the oldest known occupational diseases. The compound has also been classified as a Group I carcinogen (Carcinogenic to Humans) by the International Agency for Research on Cancer (IARC, 1997).[7]
Chronic silicosis can remain undetected for years or even decades. It is a cumulative and often fatal condition, and as it progresses, symptoms typically include shortness of breath, cough and weakness. Over time, the body’s ability to fight infection is compromised and victims become susceptible to other illnesses, such as tuberculosis. Affected individuals frequently experience fever, weight loss, chest pains and eventually respiratory failure. Exposure to crystalline silica has also been linked to lung cancer, kidney disease, reduced lung function and other disorders. Despite such recognition as a significant health hazard, it’s been estimated that 15,000 people have died from the effects of silicosis over the last two decades in the U.S. alone, and hundreds more continue to be afflicted each year. At least 1.7 million workers are thought to be potentially exposed to respirable crystalline silica, many in concentrations that exceed limits defined by current regulations and standards.[8]
Because of its widespread appearance in nature and as a fundamental building block for structures and roadways, there is ample opportunity for exposure to crystalline silica in construction and demolition operations. In fact, it is one of the most abundant naturally-occurring compounds on earth, a common component of sand, rock/stone, clay, concrete, masonry and paint. Any activities that involve the cutting, breaking, crushing, drilling, grinding or blasting of these materials may produce fine silica dust, though it can also be found in soil, mortar, plaster, shingles and abrasives.
Watch how a dust control cannon helps move towards silica dust compliance!
DUST CONTROL MITIGATION TECHNIQUES
The most common methods for controlling demolition dust are surface wetting and airborne capture. With surface suppression, the goal is to prevent dust problems by wetting the source before particles can become airborne, usually with hand-held hoses or movable sprinklers. (See Figure 1.) While these tactics can help reduce the amount of migratory dust, they tend to saturate target surfaces, often creating standing water that can become an additional safety concern or environmental hazard. In addition, their reach is generally limited, and either approach frequently requires significant staff time to man the hoses or reposition sprinkler heads. Neither technique delivers a meaningful effect on airborne particles, and both add unnecessary weight and moisture content to the debris.
Airborne dust capture techniques usually fall into one of two groups: electrostatically charged fog or atomized spray. With an electrostatic fog system, the goal is to produce extremely small water droplets with an opposite electrical charge from the airborne dust, resulting in greater attraction and particle control. Unfortunately, the method is far better suited to permanent indoor locations than constantly changing outdoor job sites. Fog systems generally do not perform well in windy or turbulent conditions and typically achieve very little surface wetting.
Atomized spray techniques also rely on the principle of creating very small water droplets, but in contrast to fogging systems, they are launched from a powerful fan at moderate to high velocity, facilitating a collision with airborne dust particles to drive them to the ground. The method has proven very effective in demolition applications, one of the few technologies capable of delivering dust control by surface wetting AND airborne particle capture.
Figure 1: Surface wetting can prevent dust on surfaces from becoming airborne; however, once the wetted material is broken during demolition, dry surfaces are exposed, again creating the potential for airborne dust.
DUST CONTROL EQUIPMENT DESIGN
Achieving effective dust suppression with an atomized spray requires that each component be engineered to work in concert with all the others to deliver the right combination of droplet size, water pressure, air flow and velocity. As airborne dust particles and water droplets approach each other, the greatest attraction is created when the particles and droplets are roughly the same size, avoiding a slipstream effect that allows droplets and particles to drift past each other without contact. (See Figure 2.) Not surprisingly, there is a tradeoff. Larger droplets will travel farther before losing their momentum, while smaller droplets are more effective at trapping airborne dust. Testing and experience have shown that the most efficient droplet size range is roughly 50-200 microns, given the apparently conflicting goals of maximizing both particle capture and coverage area.
Figure 2: When atomized spray control systems produce droplets approximately the same size as airborne particles, they deliver a greater attraction between droplets and dust.
Velocity is another critical factor, affecting range, droplet size and surface wetting. Typically, higher air velocity produces smaller droplets and better wet-out, so a powerful fan is an advantage. But even when moved at great speed, small droplets don’t carry as far as large ones, so equipment engineers must design for a balance of both desirable properties. The nozzles must also be developed specifically for dust suppression to deliver the proper spray angle and pattern to achieve optimum distribution.
Watch how Atomized Mist works above!
Atomized spray equipment is proving to be an extremely versatile dust suppression option for demolition applications. Most designs are based around an electric motor, with smaller units often running on standard single-phase power and a garden hose water supply. Larger models often require 3-phase service and are fed by a fire hose. Some suppliers are offering modifications that increase utility even further, such as an optional steel pipe tower that allows users to mount dust control systems and increase dust coverage. Larger designs will sometimes have booster pumps that can increase just 10 psi (0.7 kg/sq. cm) of water pressure to 150 psi (10.55 kg/sq. cm) or more, which has a direct impact on performance.
Some contractors have taken versatility to a new level in order to more effectively address demolition dust, custom-modifying standard equipment to serve specific applications. At least one inventive firm has designed a self-powered, trailer-mounted dust control system that matches high-efficiency, fan-driven equipment with its own generator. (See photo 1.) The dust control system incorporates a fully functional, oscillating dust suppression unit, complete with booster pump and adjustable elevation. The dust management trailer has a custom 3-phase, 480V generator on the front, with roadworthy tires for mobility.
Photo 1: Providing mobility and ease-of-use are self-powered dust control systems.
For site-specific applications, some manufacturers have developed tower mounts that allow users to improve targeting and delivery to high-dust areas, while freeing up space for vehicle traffic or other equipment. (See photo 2.) The tower-mounted dust suppressor uses remote control for convenient operation, while retaining full oscillation capabilities over a wide coverage area.
Photo 2: The dust suppression tower mount design delivers precise targeting while freeing up ground space for vehicles and other equipment, while retaining key features such as remote control and oscillation.
Another demolition company’s engineers have outfitted a boom-mounted suppression system that allows crews to significantly extend the unit’s reach and effectiveness in high-rise applications, even as a structure is being demolished. (See photo 3.) The versatility and mobility of the technique helps prevent particles from becoming airborne and reduces migration with its highly accurate delivery.
Photo 3: A boom-mounted suppression system allows crews to significantly extend the unit's reach and effectiveness in high-rise applications.
The effectiveness and versatility of the atomized spray systems have gained popularity among demolition firms, representing a truly portable dust control option that delivers greater suppression efficiency than much larger fixed systems or manual spraying techniques, at a fraction of the cost. As public awareness and industry regulations in Europe and the U.S. become more focused on reducing the risks associated with demolition dust, C&D contractors are finding that effective suppression is no longer a luxury, but a critical element of virtually every project in urban and suburban environments.
Edwin Peterson, CEO, Dust Control Technology; Mark Shaurette, Ph.D., Assistant Professor, Building Construction Management Dept., Purdue University; David Clarke, Managing Director of CDC Demolition, Past President and Honorary Life Vice President of NFDC
REFERENCES
- D’Agostino, B., Mikulis, M., & Bridgers, M. (2007): FMI & CMAA Eighth Annual Survey of Owners; Raleigh, NC: FMI.
- Safeguarding Health in Construction Work, by M.R. Trice, Industrial Hygienist, Division on Industrial Hygiene of the NC State Board of Health and the NC Industrial Commission, Presented at the annual meeting of the NC Section, American Society of Civil Engineers, January 10, 1942, Duke University, Durham, NC, 11 pages, typewritten.
- “The More We Learn, the More Things Stay the Same: Notes On a Pioneer In Occupational Safety and Health,” Jane L. Seegal and John C. Lumsden, downloaded from www.cdc.gov/elcosh/docs/d0100/d000015/d000015.html on 8/15/08.
- From interview with Lou Gherlone, Spring Street Recycling, West Haven, CT, November 19, 2007.
- Heymann DL, ed. (2004). Control of communicable diseases manual. 18th ed. Washington, DC: American Public Health Association, pp. 273-275.
- Lenhart, S., Schafer, M., Singal, M., & Hajjeh, R. (2004): Histoplasmosis: Protecting workers at risk; Cincinnati, OH; National Institute for Occupational Safety and Health.
- OSHA Instruction (Directive CPL 03-00-007, National Emphasis Program – Crystalline Silica, effective January 24th, 2008.
- NIOSH Hazard Review: Health effects of occupational exposure to respirable crystalline silica; Cincinnati, OH: U.S. Department of Health and Human Services, Centers for Disease Control and Prevention, National Institute for Occupational Safety and Health, DHSS Publication No. 2002-129.
STOP DEMOLITION DUST WITH DUST CONTROL TODAY!
Receive a FREE quote and talk to a dust control specialist today to end fugitive dust!