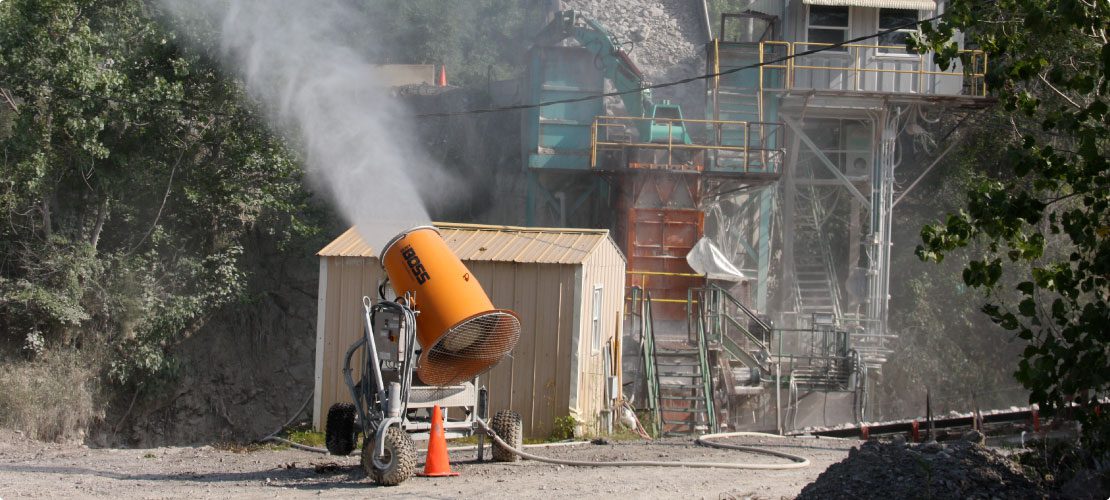
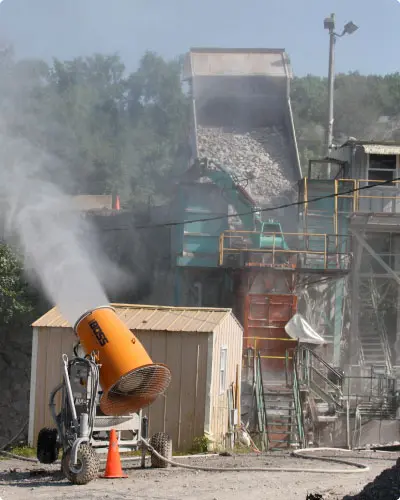
For Linwood Mining and Minerals Corporation in Davenport, Iowa (US), every hour of downtime means thousands in production dollars lost.
An electronic monitor constantly assesses the air quality in the area of the mining operation and forwards the readings to Linwood and to the Iowa Department of Natural Resources.
"The DB-60 unit paid for itself within one month of use due to eliminated downtime."
Jim Gilliam - Mine Manager
In order to maintain compliance with government air quality standards, dust emissions from Linwood’s plant and other production facilities in the surrounding area must stay within a specified range of values over a 24-hour period. If the readings exceed the specified range due to excessive dust, the facilities must shut down.
In operation since 1944, the company is one of the largest underground mines in Iowa and ranks among the largest limestone mining operations in the U.S.. Linwood operates 5-1/2 days a week, year round, to produce more than one million tons of limestone a year.
Once brought to the surface, the limestone is run through the primary crusher and reduced to 5" or less material. The crushed material is then put on the surge pile where it is taken to the secondary crushing plants on the site to be reduced down to a variety of sizes.
MINING DUST CONTROL
In the past, Linwood has used water hoses and spray bars to help control dust both at the crusher and at transfer points. On average, due to excessive dust emissions, the plant experienced a substantial amount of downtime each month.
Not only were the hose and spray bar methods ineffective, they also oversaturated the material, making it sticky, muddy and difficult to handle during the finishing process. More importantly, quality is an issue because use of dirty material inherently contributes to the failure of the end product, creating air pockets in asphalt and causing cracking or pop-outs on the surface of finished concrete.
After seeing the DustBoss at ConAgg/ConEXPO early in 2008, Linwood Mining decided to rent a DB-60 on a trial basis. The unit was set up to run over the primary impact crusher used on the site, a Universal 4650.
Immediately, management at Linwood observed an improvement in dust control—in addition to a considerable increase in the quality of the crushed limestone—and decided to purchase the unit.
The DB-60 dust suppression unit paid for itself within one month of use due to the marked decrease in downtime, according to Jim Gilliam, Mine Manager. Before purchasing the unit, the plant experienced several periods of downtime a week, resulting in lost production time. Since implementing the DustBoss at their site, Linwood has not experienced any downtime due to their plant’s dust emissions.
“The portability of the unit and our ability to direct the mist as needed makes it more flexible than other options when dealing with the wind," said Gilliam.
"The unit's performance and low maintenance have definitely met and even exceeded our needs."
Jim Gilliam - Mine Manager
Production Manager Jim Petersen adds, “Some material is dustier than others, depending on the mine horizon. We’ve run the unit over the dustiest materials we process...it’s done exactly what we’ve needed it to."
IMPLEMENT DUST CONTROL AT YOUR JOB SITE!
Receive a quick quote and talk to a dust control specialist today to end fugitive dust!